Turnkey Projects
With more than 20 years of experience in running medium to large projects our Management Staff have the skills to assist you with your project; from planning and project engineering through to procurement, prototyping, manufacturing, installing and commissioning.
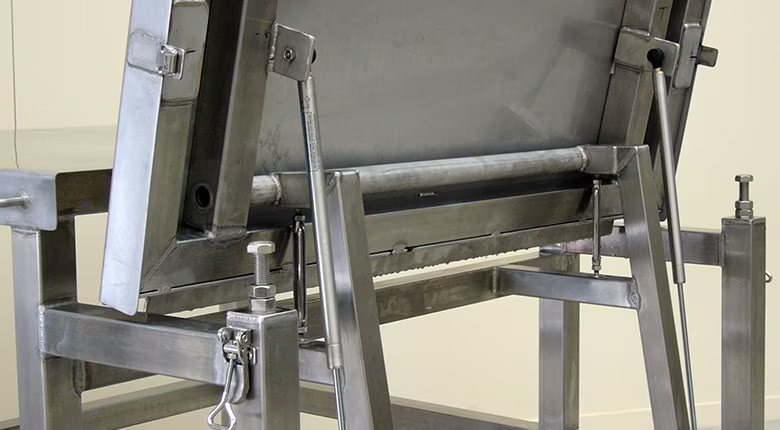
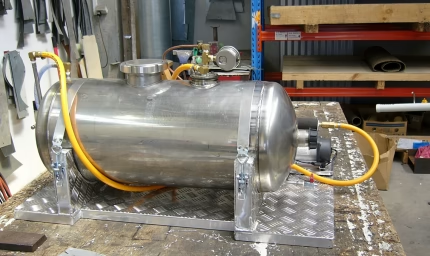
If your project or product is new or innovative we will happily sign a confidential agreement to ensure that any and all Intellectual Property remains with you – our client – and ensure that the project is completed with care and discretion.
Projects completed include
- Boning Room Table System – this project involved an in-house assessment of existing production processes to develop a new table system capable of multi-functions whilst remaining generic to the existing requirements of the production line. In doing so it had to incorporate improvements in the meat handling process and in particular reduce the number of repetitive strain injuries being experienced. An added difficulty was the need for the table to “open up” at smoko and lunch breaks (or during an emergency) to allow staff to leave the production area without climbing under or over the tables as they had been doing. A new ergonomic design solved these problems. The project was completed in 8 weeks and was under budget.
- Pollen Dispensing System for Kiwi Fruit Industry – we worked with the original inventor of this product to turn it into an item ready for multiple-unit production. This project required careful attention to the overall weight and centre of gravity of the finished product whilst retaining its ruggedness to withstand its harsh operating environment. After the project, more than 12 units were made with different configurations for motorbike and tractor operation. We are still supplying units to this day.
- Blood Plasma Extraction Room – we have completed the full design, manufacture, installation and commissioning of 2 rooms involved in processing meat and by-products within the Freezing Works industry. In both cases, we worked closely with the client to ensure their requirements from initial to final processed product through each workstation met or superseded their production targets. These projects involved time management, production process and bottleneck studies to ensure production targets were met whilst improving workplace safety and comfort. The production process was very physical and required an ergonomically designed solution. Items manufactured include:- tables and benches, chutes, overhead rail systems, pneumatically operated gates and chutes. The project also included all electrical work including control systems. Both rooms were fitted with safety equipment including motion and location sensors to ensure worker safety.
Showcasing Our Expertise:
Turnkey Sheetmetal Projects
Explore our gallery of our turnkey sheetmetal projects.